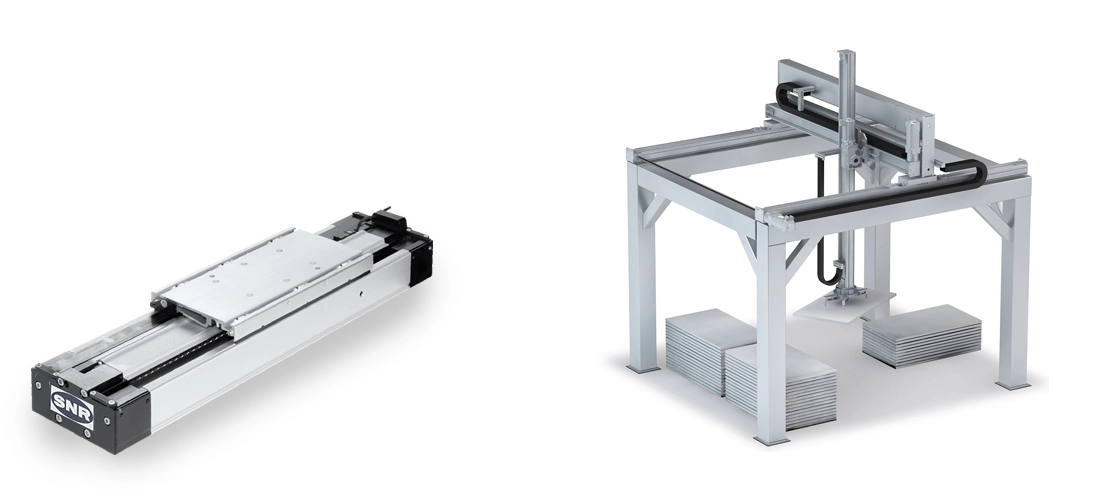
Linear axes, linear tables, linear modules for precise linear systems
Linear axes and linear tables for precision results with high dynamics
We are happy to calculate an axis or even an entire system of linear modules for a wide range of applications and with various equipment options. Our linear modules are driven by ball or trapezoidal screw drives - optionally also with toothed belts or racks. Profile rails or rollers ensure the correct guidance. At Lenze, you don't just get the axis as a component. We also support you in the selection of geared motors, including servo technology and controllers, right through to programming the control system and commissioning. This gives you an optimally coordinated handling system. With us, you can realize your gantry robot quickly and easily!
Drive systems
Depending on the series, the linear axes are manufactured with toothed belt drive, spindle drive, rack and pinion drive and linear motor drive. Each drive system has certain advantages and disadvantages. Toothed belt drives, for example, are particularly suitable for fast positioning. Spindle drives, for example, have a high positioning accuracy. Depending on your requirements, the loads to be transported, the required speeds and the forces that occur, we will support you in selecting the right linear axes and systems.
Toothed belt drive
Linear axes with toothed belt drive are suitable for fast handling and positioning tasks. All axes are equipped with AT or STD timing belts. These are extruded polyurethane belts with integrated steel tension members.
These timing belts are also characterized by the following properties:
- Low wear
- Maintenance-free
- High tensile strength and low elongation
- Very high accuracy - pitch error ± 0.2mm/m
- UV-resistant
- Temperature range -10° to +75°C
- Low noise
- Versions with approval for the food industry
Spindle drive
Linear axes with screw drives can be equipped with both ball screw drives and trapezoidal screw drives. Spindle drives are particularly suitable for high positioning and repeat accuracy requirements in combination with high rigidity of the drive element.
The drive can be adapted directly via a coupling and coupling bell or via an idler belt drive.
Advantages:
- Large travel ranges with high positioning accuracy
- Very long travel distances can be realized through the use of spindle supports
- Choice of different spindle pitches
- High feed forces
- High drive rigidity
- No gearbox required in some cases
Rack drive
Linear axes with rack and pinion drive are characterized by very high operational reliability and are therefore particularly suitable for vertical applications. Any number of rack and pinion segments can be connected in series.
The induction-hardened racks and gear wheels guarantee a very long service life.
Advantages of the drive:
- Theoretically unlimited lengths possible
- Several drive units possible
- High feed forces
- Maximum drive rigidity even with high loads
Guide systems
Depending on the series, linear axes can be equipped with linear guides or various types of roller guides. These selection options make it possible to react extremely flexibly to the requirements of the application and the ambient conditions and to select an optimum configuration of the linear axes. If linear axes are used purely as a drive element, a design without guide elements is also possible.
Linear guides
Linear axes of all series are equipped with linear guides with integrated ball chain. Due to the arrangement of the raceways at a 45° angle, the linear guides can be used universally and have the same load ratings in all main load directions. The special features of our linear guides with ball chain include the integrated lubricant reservoirs.
The use of these linear guides offers the following advantages:
- High load ratings
- Long service life
- Long-term maintenance-free
- High tolerance compensation and error compensation capacity due to X arrangement of the raceways
- Low noise level
- Very smooth running
- High speeds up to 5 m/s
- High accelerations up to 50 m/s²
Roller guide
Depending on the series, different types of track rollers can be used for the track roller guides.
All sizes in the AXC series are available with steel roller guides. This system consists of track rollers that roll on ground, hardened steel shafts incorporated into the aluminum profile. The steel shafts are permanently lubricated from an oil reservoir that can be refilled from the outside. The rollers are dust-protected, double-row angular contact ball bearings with a profiled outer ring. Thanks to the eccentric bearing of half of the rollers, the guide system can be precisely adjusted and therefore always has the correct preload and freedom from play at the factory.
This technology ensures excellent running properties and offers the following advantages:
- Very cost-effective guide system, especially for long lengths
- Long service life thanks to the use of dust-protected bearings and the internal arrangement of the rollers in the profile
- Very high speeds of up to 15 m/s
- High accelerations of up to 50 m/s²
Polymer rollers
Linear axes from the AXF series can also be fitted with polymer rollers as an option. In this variant, the rollers run directly on the surfaces of the aluminum profile. The preload is adjusted via a spring element in the two-part carriage unit during assembly. The polymer rollers are mounted on plain bearings on the carriage unit. Linear axes with this guide system can also be used in wet areas, with heavy soiling or in conjunction with aggressive media.
This guide system is characterized by the following features:
- Very high media resistance
- Maintenance-free and dirt-resistant rollers
- Good mechanical damping properties
- Internal arrangement of the rollers
- Very high speed up to 7 m/s
- Accelerations of up to 30 m/s²
Selection criteria for linear axes
Below you will find a list of important selection criteria for linear axes. For optimum design and selection, please contact our experts at: engineering@lenze-selection.com
Dynamics
Dynamics are an important criterion when selecting a suitable axis system. The acceleration, the speed and the travel cycle have a significant influence on the drive system, the guides and the axle types.
Masses and center of gravity
Not only the mass to be moved, but also the center of mass is important when selecting and dimensioning the axle system. Depending on the arrangement, this can have a considerable influence on the stability and size of the axles.
Repeatability
With repeat accuracy, any point is approached several times from one direction from the same starting point and the deviation from the target value is measured. The process is repeated for different points. ± 50% of the difference between the maximum and minimum deviation is specified as the repeatability.
Positioning accuracy
When measuring the positioning accuracy, several points are approached in one direction and the difference between the target distance and the actual distance traveled is measured. The positioning accuracy is the absolute maximum difference.
Parallel running
A dial gauge mounted in the center of the slide unit is moved over the entire stroke. The running parallelism is the maximum difference between the readings.
Backlash of ball screws
The carriage unit is moved against a dial gauge as a reference point using the ball screw drive. The carriage unit is then loaded in the same direction by an external force and then unloaded. The backlash is the maximum difference between the reference point and the position after loading and unloading.
Our linear axes for industrial applications
AXC – The versatile
AXC compact axes are particularly suitable for light and medium loads up to approx. 250 kg. They offer a wide range of variants and options. With toothed belt drive or spindle drive, different guide systems and a wide range of attachment options, individual requirements can be met.
AXE – The Standardized
The standardized modular system ensures high availability, short delivery times and low prices. The axes are available from stock in defined lengths and with various mounting options and can be supplied as individual axes or as a complete system.
AXDL – Double is better
These parallel axes (parallel guide system of either linear guides or track rollers) are ideal as a rigid single axis or in combination with other axes from our portfolio.
AXLT – The robust one
Linear tables are particularly suitable for high loads and torque loads. The linear tables have either a ball screw drive or trapezoidal screw drive and two parallel linear guides as a guide system.
AXS – Axes with system
The AXS series are our system program axes for the highest loads as telescopic, lifting, beam and portal axes. The AXS has linear guides as guide systems and can be driven by toothed belts or racks.
Multi-axis systems - the all-round carefree package
Together with Lenze, we can not “only” calculate and supply the axes. Thanks to our drive and automation technology know-how, we (Lenze Selection & Lenze) can offer a complete system. Starting with the linear axes, drives and controllers through to automation solutions and commissioning.